2024.02.24
はんだ付け品質改善活動の進め方について
今回は、はんだ付け品質改善活動の進め方について、1990年代の筆者の経験をもとに説明します。電機メーカー在籍時にトップダウンにより「修理サービスデータを見るとはんだ付け品質が悪い!!」と緊急の改善指示があり、全社(設計、品質、製造工場)及び製造委託先を含めて改善活動を進めることになりました。修理サービスデータを分析すると製品により異なりますが不良品のなかで製造、設計&部品要因がそれぞれ30%以上あり、製造要因の中でもはんだ付けに起因する不具合が多いというデータでした。おそらく、製造工程の中で検出できない潜在的なはんだ付け不良(フレット小、異物付着、ストレス印加など)が検査工程をすり抜けて市場流失してしまい初期不良として発現したものと考えられます。日頃の実装技術部の業務活動の中で試作から量産における設計改善やはんだ付け状況をウォッチしてはいましたが不足していたという証拠でもありました。そこで活動を進めるにあたり、実装技術部がリーダーシップをとり、活動組織:はんだ付け品質改善委員会を立ち上げて、現行はんだ付け品質データの採取&分析及び設計部門、製造条件へのフィードバックを行うというフローを構築しました。活動内容の概要は下図の通りです。
【品質改善委員会の活動内容】
・試作量産におけるデータの採取~要因分析~設計&製造へのFB:はんだ付け品質の悪い機種を数モデル選定して、はんだ付け直後のデータ(素上がり品質)を採取&要因分析して設計、製造へフィードバックして改善を進めるフローです。
・はんだ付け条件の設定管理、活動目標の策定、品質改善委員会開催
この活動を本社圏工場(国内1海外工場4)で2年間実施して工場担当者の意識改革、品質改善の効果を確認してから中国の製造委託先5社(1,000~3,000人規模)へはんだ付け品質改善活動を展開しました。この内容は次回に説明します。そして、4年経過後の修理サービスデータを調査すると明らかにはんだ付け要因による不良の大幅な改善が見られました。はんだ付け要因の不良が改善されたので全体の不良率も大幅に改善しました。機種により異なりますが、不良率が数%あったものがほとんどのモデルで0.1%以下となったのです。※不良率:不良数/総販売台数
以上、これからはんだ付け品質改善活動を実施したいと考えているお客様では参考にして頂けると幸いです。また、弊社の技術サポートも可能ですのでHPまでご連絡いただきたく宜しくお願い致します。
お客様の状況にあった改善委員会を組織し「はんだ付けデータ採取~要因分析~設計&製造へのフィードバック改善」フローの構築&実践がポイントです。
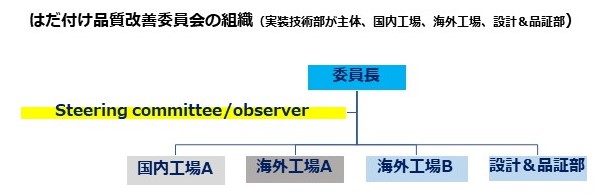
※各工場では実装Gが主体となり、製造G、品証Gが連携して活動する
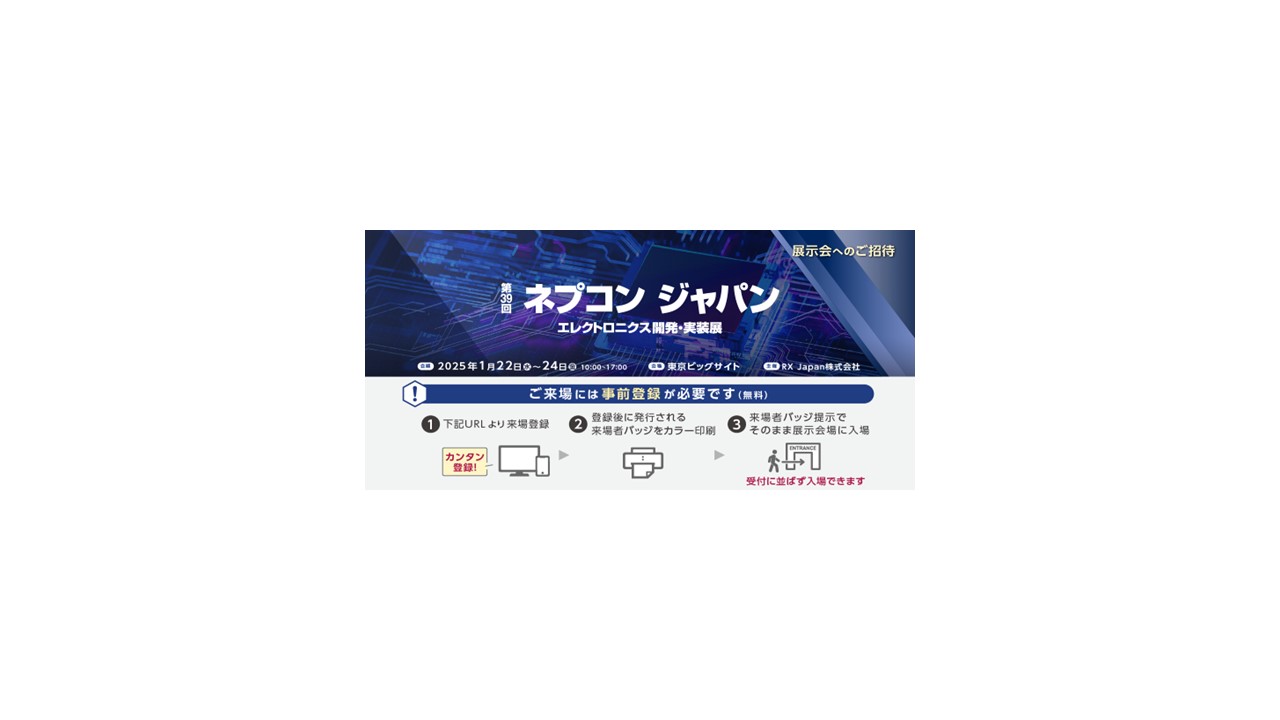
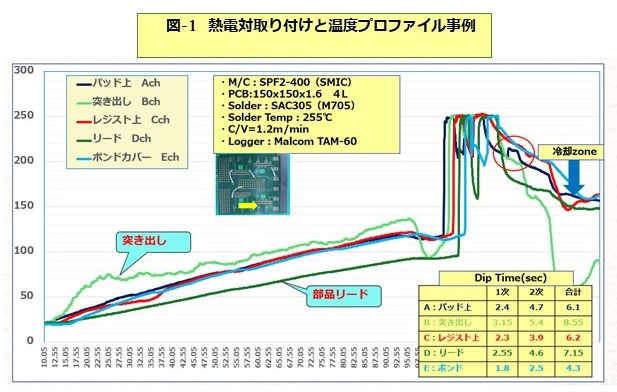
関連記事こちらの記事も合わせてどうぞ。
2025.02.19
コラム記事(No.48)「業界各社のはんだ付け条件」について
2025.01.25
コラム記事(No.47)「電気製品の市場不良」(Ⅲ)について
2024.12.14